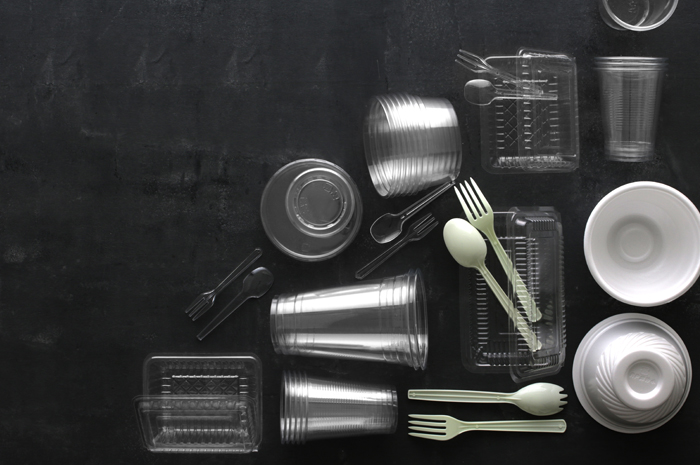
プラスチック容器の主な成形方法
フードパックやどんぶり容器、青果容器、寿司容器などスーパーやコンビニには、様々な形の容器が並んでいます。浅い形から深い形、角のあるものから丸いものなど、それぞれ使用する食品に合った形・特徴のある容器が使われています。
では、それぞれ容器はどのように作られているのでしょう。
どんな形の容器も製造方法は同じなのでしょうか。
今回は、意外と知られていないプラスチック容器の主な成形方法について2つご紹介していきます。
プラスチック素材について
成形方法についてご説明する前に、まずはプラスチックの素材についてご説明していきます。
プラスチックとは、熱や圧力を加えることにより成形加工のできる合成樹脂です。
特にトレー成形には、加熱や圧力によって柔らかくなり、冷やすと硬くなる特徴を持つ「熱可塑性樹脂」が使われています。身の周りに溢れている硬さ、質感、形などが多種多様なプラスチック製品は、成形工程での圧力、熱によって生み出されます。
ここからは、食品容器の代表的な成形方法とされる真空・圧空成形、射出成形の2つについてご説明していきます。
お弁当容器・フードパックを作るときは「真空・圧空成形」
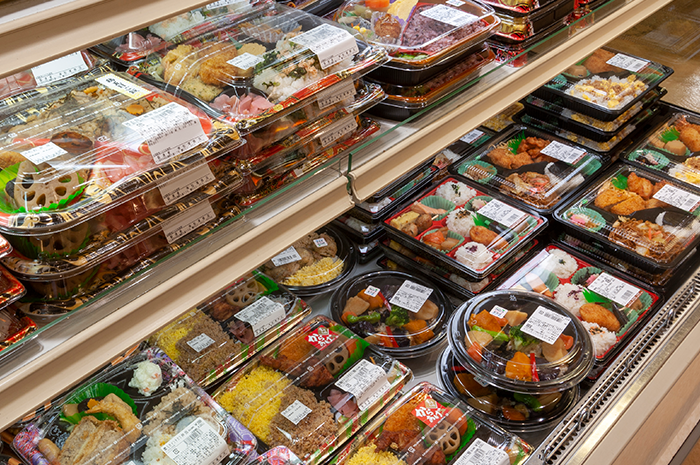
まずはじめに、真空・圧空成形について紹介します。
真空成形、圧空成形とは、フィルムやシート状の樹脂素材を加熱軟化させ、型に密着させ成形するプラスチック使い捨て容器の代表的な成形方法です。
真空・圧空成形で作られる容器としては、フードパックやお弁当容器、発泡トレーなど浅型の容器が多く、またお弁当容器の蓋なども代表例の一つです。
真空圧空成形では、短時間に大量の製造が可能なため、大量生産が必要とされるフードパックやお弁当容器の成形に向いているといえます。
また、ほかにも2つを組み合わせた真空圧空成形もあります。
ここからは、真空・圧空成形の製造工程や用いられる素材、真空成形と圧空成形の違いなど、詳しくご説明していきます。
ペレットから原反シートへ
プラスチック容器の元になる原料はペレットと呼ばれる3mm程度の粒状の合成樹脂です。
まず、ペレットを加熱し、軟化させシート状に押し出します。押し出されたシートを冷やしながら、均一の厚みになるように整えます。
整えられたシートは巻き取られ、原反と呼ばれる加工がされていない容器の元となるロール状のシートが完成します。
真空圧空成形
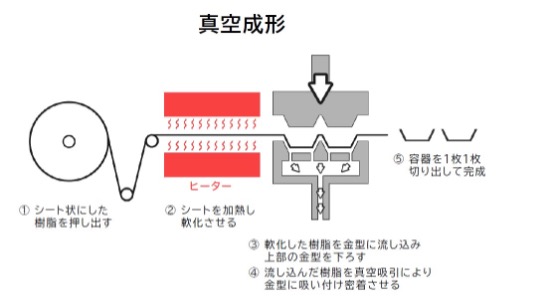
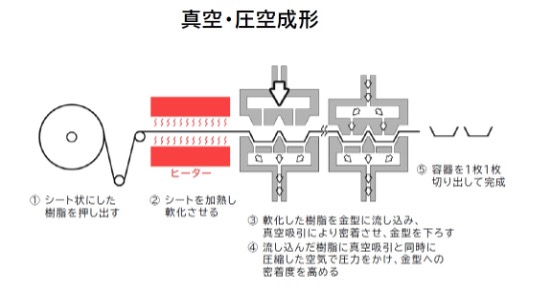
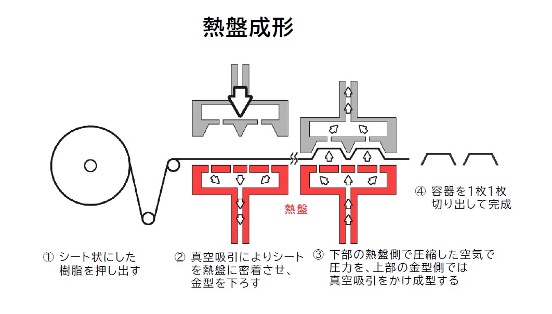
次に、成形工程に移ります。
先程の原反シートを加熱し、軟化させ、金型や熱盤を用いて成形を行います。
この成形の工程は初めにもお伝えした通り、真空成形、圧空成形、2つを組み合わせた真空圧空成形の3つがあります。真空成形の場合は、金型に空いている微小な孔からシートと金型の隙間の空気を吸い込み、真空状態にして金型に密着させ、冷却、硬化をすることで成形を行います。食品容器の場合、凹凸両方の金型で真空状態にして成形する場合が多く見られます。
適合素材としては、PSPなどの発泡素材が挙げられます。
圧空成形の場合は、軟化させたシートに対して、圧縮空気を送り込みながらシートを金型に密着させ、冷却、硬化をすることで成形を行います。
適合素材としては、OPSなどがあり、伸びにくい素材に適しています。
2つを組み合わせた真空圧空成形の場合は、軟化させたシートに対して、上からは圧縮空気を送り込みながら金型を密着させ、下からは金型に空いている微小な孔からシートと金型の隙間の空気を吸い込み、真空状態にして、成形を行います。
適合素材としては、PETやPPFなどがあり、固い素材に適しています。
抜き工程
次は抜きの工程に移ります。
成形されたシートは、この抜き工程で余分な周りの部分を落とし、容器の形へ打ち抜かれます。
例えると、クッキーの型抜きのようなイメージです。この例からもわかるように、成形されたシートはすべて容器となるのではなく、周りに必要な部分を切り取った残りである端材ができます。
成形から抜き工程まで、ほんの数秒で完了する場合がほとんどです。
端材を再利用する場合も
抜き工程で、周りの余分な部分として端材になったプラスチックは、熱を加え液状に戻され、再びペレットに戻し再利用する場合もあります。
これを行うことで、プラスチック資源のロスを最小限に抑えることができます。
デザートカップ、カトラリーをつくるときは「射出成形」
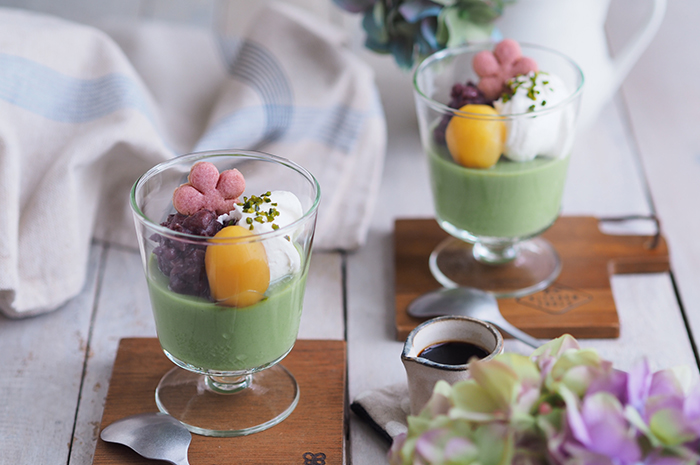
次に、射出成形についてご紹介します。
射出成形とは、金型を用いた成形方法の1つで、プラスチックなどの材料を加熱し溶かし、金型に送りこんだ後、冷やすことで目的の形をつくる成形方法です。別名インジェクション成形とも呼ばれます。
射出成形に用いられる主な素材には、ポリプロピレン(PP)、ポリエチレン(PE)、ポリスチレン(PS)などがあります。また、射出成形で作られる容器としては、ゼリーカップなどの足つきの容器や、尖りや丸みなど細かいデザインが必要なカトラリーなどがあります。
射出成形では、型によってさまざまな形の形状を成形できるため、真空・圧空成形に比べ、製造できる容器・資材の幅が広いのも特徴の1つです。食品資材にだけでなく、自動車部品、医療用機器など繊細なデザインが求められる分野でも使われていることからも射出成形の幅の広さがうかがえるでしょう。
ここからは、射出成形の製造工程について、詳しくご説明していきます。
ペレットを溶解させる
射出成形も真空・圧空成形と同様に、ペレットが原料となります。
まず、ペレットをシリンダーの外周に取り付けられているヒーターで、約200~300℃の高温で加熱し、シリンダー内で液状の軟化状態にします。溶けた原料は、一定量、シリンダーの先端に溜められます。
金型で成形
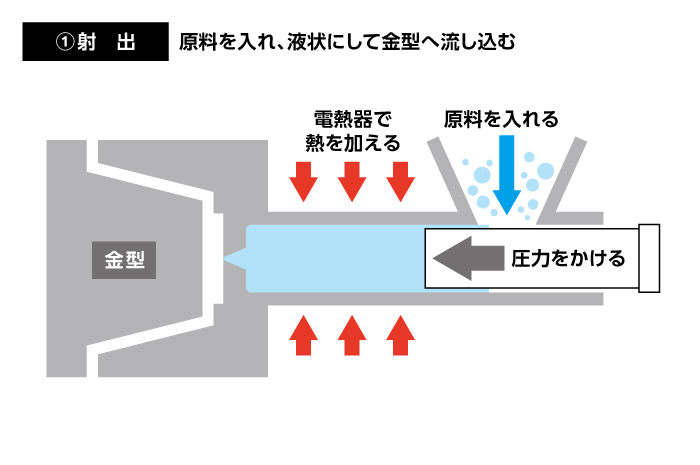
次に、液状の原料を、注射器のように圧力をかけながら、金型の中に流し込みます。
このとき金型は閉じた状態で凹と凸がかみ合っている部分の間に流し込みます。そうすることで、金型に沿って原料が固まっていき、欲しい形の容器が得られます。
射出成形では、この金型の形を変えることによって、細かいデザインのある容器や、フォークの先などの尖り、デザートカップなどのような足のある容器など様々な形の製品を製造することが可能になります。
これが、真空・圧空成形との大きな違いです。
保圧、冷却、型開き工程

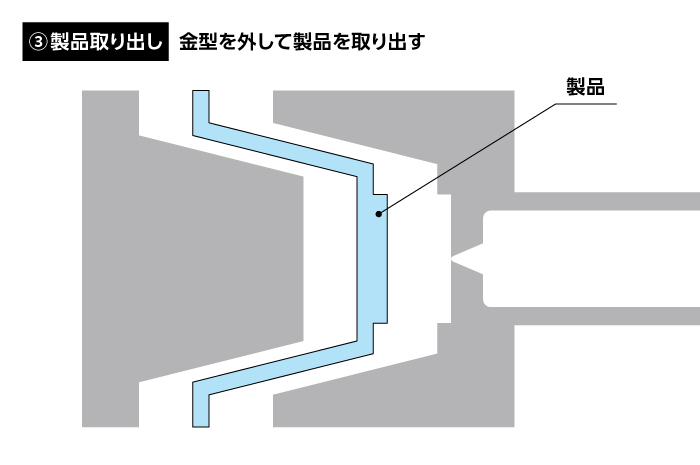
原料を金型に流し終えたら、すぐに型を開くのではなく、流し込まれた樹脂に一定時間、圧力をかけ続けます。この工程を行わないと、成型時に収縮してしまい、割れや欠けなど不良品になってしまうリスクが高まります。
一定時間圧力をかけ終えたら、型を冷却させ、流し込んだ原料を固化させます。原料が完全に固まったら、型を開き、製品の成形が完了します。
各成形方法のメリット・デメリット
ここまで、真空・圧空成形、射出成形の工程についてご説明してきました。
当たり前に身近に溢れている食品容器や資材も私たちの手元に届くまでに、たくさんの工程を経てたどり着いていることが感じられたのではないでしょうか。
次に、各成形方法のメリット・デメリットをご紹介します。
「新しいメニューの提供の際、容器を新しく作りたい」「期間限定商品で違う形の容器が欲しい」など何か容器を作るとき、探すとき、成形方法のメリット、デメリットを知っておくことで、イメージに合った容器探しのヒントになるかもしれません。
真空・圧空成形のメリット・デメリット
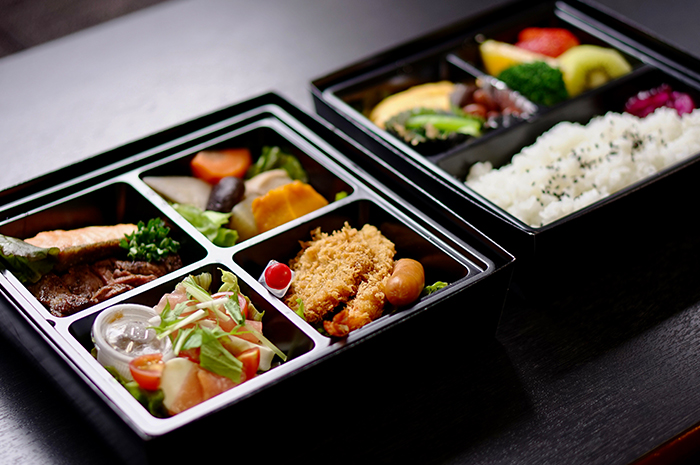
メリット
大量生産に向く
形や大きさにもよりますが、通常の場合、同じ形状の金型を数個組み合わせ、大きな金型を作成し、成形をする場合がほとんどで、成形から抜き工程までほんの数秒で完了します。そのため大量生産に向いていると言えます。
射出成形に比べコストが安価
単純な作りでの製造が多いため、金型製作の費用も射出成形に比べ通常、安いのが特徴です。木型でも製造可能な場合もあるため、より価格を抑えることもできます。
デメリット
深い形の成形や、細かい精度が求められる成形には向かない
プラスチックのシートを引き延ばして成形するため、深い凹凸を作れず、また温度変化で微妙に寸法が変化するため射出成形に比べ精度が出にくい点が挙げられます。
射出成形に比べ、原料のロスが多い
射出成形は、必要な量を型に流し込み成形をするのに対して、真空圧空成形ではシートを製品の形に打ち抜いて成形するため、端材が出てしまいます。そのため前述の通り、端材を工場内でもう一度ペレットに戻し、端材として出さないように取り組む場合もあります。
射出成形のメリット・デメリット
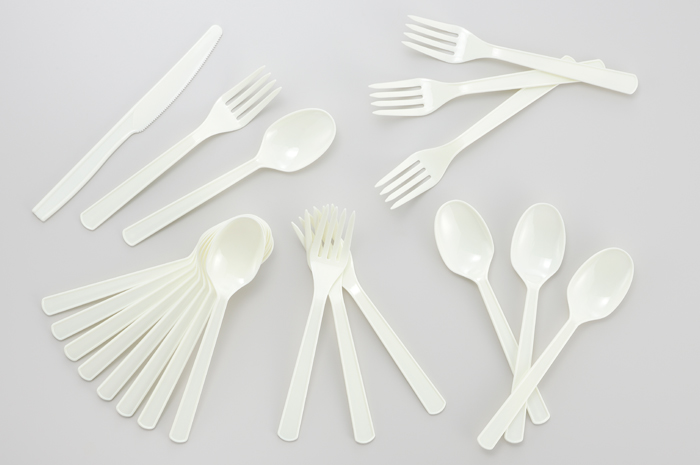
メリット
複雑な形もデザインが可能
射出成形の1番のメリットは、複雑な形へ対応ができる点です。
デザートやドリンクカップの足や、どんぶりなど深さのある容器、カトラリーなどの複雑な形だけでなく、店名などロゴマークの印字などより細かいデザインも作成できます。
原料のロスが少ない
真空圧空成形ではシートの端が余ってしまうのに比べ、必要な分だけ、原料を金型に流し込み成形を行うため、原料のロスが少ないというメリットもあります。
デメリット
少量生産には向かない
複雑な形のデザインが可能というメリットの反面、その分金型の製作にコストと時間がかかってしまいます。金型代が上がる分、製品単価が上がってしまうため、少量生産にはあまり向きません。
不良品リスクが真空圧空成形に比べ高い
より複雑な形状の製品の作成が多いため、バリや割れなど、真空圧空成形に比べ、不良品のリスクがどうしても高まってしまいます。金型や機械の劣化に伴い、不良品のリスクが高まってしまうため、定期的な点検、交換が必要です。
成形方法を知ってぴったりな製品を選びましょう!
真空・圧空成形 | 射出成形 | |
---|---|---|
製品例 | お弁当容器・フードパック | カトラリー・デザートカップ |
コスト | 安い | 高い |
生産ロット | 少量対応可能 | 大きい |
原料ロス | 多い | 少ない |
デザイン性 | 制限が多い | 多種多様 |
製作時間 | 短い | 長い |
今回は、プラスチックの成形方法である真空圧空成形と射出成形についてご紹介しました。
普段当たり前のように毎日目にするプラスチック製品ですが、その特徴によって成形方法が分かれており、その製造工程の精密さや重要さが伝わったかと思います。
プラスチック製品の成形方法は今回ご紹介したものだけでなく、ブロー成形やインフレーション成形、押出成形など、他にもさまざまあります。それぞれの特徴に合わせて選択され、成形、製品化されています。普段使用しているプラスチック製品について、時には成形方法を意識してみてみると、最適な商品の選択につながるかもしれません。
今回ご紹介した成形方法で製造されたプラスチック容器をはじめ、容器スタイルでは、幅広い商品を販売しております。
ぜひチェックしてみてください。